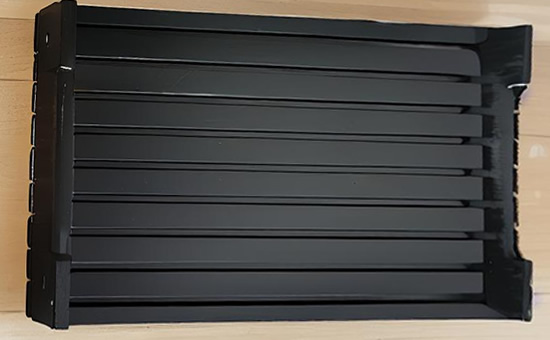
天然再生膠以廢天然膠、廢乳膠制品為主要原料加工而成的橡膠再生資源,可直接替代部分天然橡膠或與其他橡膠并用生產(chǎn)橡膠制品,有效降低原料成本。道軌減震墊即軌道減震墊或軌道隔離墊,通常由橡膠、塑料、金屬或其他合成材料制成,用于減少軌道結(jié)構(gòu)對周圍環(huán)境的振動和噪音影響。道軌減震墊橡膠部分可使用天然橡膠、再生橡膠等,天然再生膠可單獨(dú)使用或與天然橡膠并用,賦予道軌減震墊良好的彈性與耐久性。
1.天然再生膠生產(chǎn)道軌減震墊硫化配方基本組成
以天然再生膠為主要原料生產(chǎn)道軌減震墊時,天然再生膠作為基礎(chǔ)材料使用,能夠提高必要的彈性和耐久性,或者將天然橡膠與天然再生膠并用。使用炭黑作為補(bǔ)強(qiáng)劑,提高天然再生膠道軌減震墊的彈性與耐久性;天然再生膠道軌減震墊選擇硫黃或過氧化物作為硫化劑,用于交聯(lián)橡膠分子,提高其強(qiáng)度和彈性;使用石蠟油或增塑劑的軟化增塑體系,能夠有效改善橡膠的加工性能和柔韌性;防老體系的使用則可以延長天然再生膠道軌減震墊的使用壽命。
2.天然再生膠生產(chǎn)道軌減震墊硫化配方優(yōu)化技巧
衡量橡膠道軌減震墊的技術(shù)參數(shù)主要包括硬度、拉伸強(qiáng)度、撕裂強(qiáng)度、壓縮永久變形、耐磨性、耐老化性等。以天然再生膠為主要原料生產(chǎn)道軌減震墊時,需要根據(jù)道軌減震墊的具體使用要求,調(diào)整硫化劑、促進(jìn)劑的品種與用量,以及補(bǔ)強(qiáng)劑和軟化劑的比例,以達(dá)到最佳的物理性能;選擇合適的防老劑和抗氧化劑,以提高產(chǎn)品的耐候性和抗氧化性。
在實(shí)際生產(chǎn)中,不同類型的硫化劑(如硫磺、過氧化物、金屬氧化物等)對交聯(lián)密度的影響不同;硫化劑的用量增加通常會增加交聯(lián)密度,用量過多會因?yàn)檫^度交聯(lián)而導(dǎo)致橡膠性能下降。促進(jìn)劑可以加速硫化反應(yīng),不同類型的促進(jìn)劑對硫化速率和交聯(lián)密度有不同的影響。補(bǔ)強(qiáng)劑(如炭黑)和填充劑(如碳酸鈣)可以影響橡膠的硫化行為和交聯(lián)密度。軟化劑、增塑劑過量使用則會降低交聯(lián)密度。
2.天然再生膠生產(chǎn)道軌減震墊生產(chǎn)工藝流程與注意要點(diǎn)
天然再生膠生產(chǎn)道軌減震墊的最主要的流程是混煉、成型以及硫化。
混煉:是將天然再生膠與各種添加劑混合均勻。
成型:將混煉好的橡膠材料成型為所需的道軌減震墊形狀。
硫化:在一定的溫度和壓力下進(jìn)行硫化,使橡膠達(dá)到所需的物理性能。
在硫化過程中,控制硫化溫度和時間對于獲得最佳的道軌減震墊性能至關(guān)重要。硫化溫度和時間的控制可以影響橡膠的交聯(lián)密度、物理性能和耐久性。天然再生膠道軌減震墊硫化時需要確定最佳硫化溫度與硫化時間。
硫化溫度的確定通常基于所使用的硫化體系(如硫磺硫化或過氧化物硫化)以及橡膠配方。
溫度過高可能導(dǎo)致過度交聯(lián),使橡膠變硬、變脆,而溫度過低則可能導(dǎo)致交聯(lián)不充分,橡膠強(qiáng)度和彈性不足。通常,硫化溫度會在橡膠的推薦硫化溫度范圍內(nèi)進(jìn)行調(diào)整,以獲得最佳的物理性能。
硫化時間是指橡膠在硫化溫度下保持的時間,以確保達(dá)到所需的交聯(lián)程度。硫化時間過短可能導(dǎo)致交聯(lián)不完全,而時間過長則可能導(dǎo)致過度交聯(lián)。硫化時間的確定通常通過實(shí)驗(yàn)和經(jīng)驗(yàn)來優(yōu)化,可以通過硫化曲線(即硫化時間與硫化程度的關(guān)系圖)來輔助確定。
確保硫化過程中模具內(nèi)的溫度和時間分布均勻,以避免局部過硫化或欠硫化。使用適當(dāng)?shù)募訜岷屠鋮s系統(tǒng),以及模具設(shè)計(jì),以確保硫化過程中的溫度和時間控制。為了進(jìn)一步提高橡膠的性能,可能需要進(jìn)行后硫化處理,在硫化后將橡膠保持在一定的溫度下一段時間,以進(jìn)一步完成交聯(lián)。
以天然再生膠為主要原料生產(chǎn)道軌減震墊時還有很多需要注意的地方,后續(xù)我們將繼續(xù)與您討論相關(guān)話題。
獨(dú)家原創(chuàng)文章【商業(yè)授權(quán)】無書面授權(quán)禁止任何形式轉(zhuǎn)載,摘抄、節(jié)選。關(guān)注鴻運(yùn)橡膠:學(xué)習(xí)再生橡膠生產(chǎn)橡膠制品的工藝配方和原料的技術(shù),幫您降低成本增加利潤。