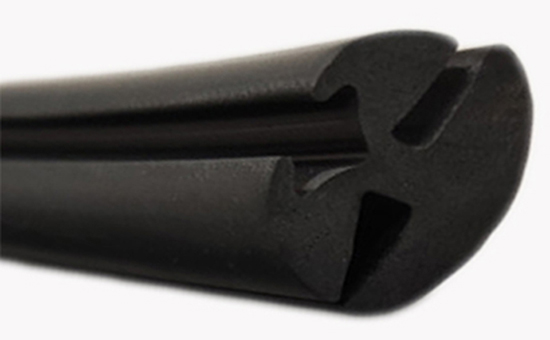
再生膠制品生產(chǎn)過程中水分含量過高會導致橡膠制品成品出現(xiàn)氣泡,影響產(chǎn)品質(zhì)量外觀與成品率,尤其是添加一些液態(tài)配合劑如松焦油、古馬隆等。因此需要嚴格控制再生橡膠制品生產(chǎn)過程中的水分含量,以免再生膠混煉時出現(xiàn)分散不均勻、硫化時產(chǎn)生氣泡的問題出現(xiàn),提高成品率,避免不必要的經(jīng)濟損失。
1.橡膠預(yù)處理:橡膠制品生產(chǎn)前對原膠、再生膠24LYY0226進行干燥處理,去除多余的水分。常用干燥機或烘房,確保膠料中水分含量降至最低。生膠在60-70℃的烘房內(nèi)烘軟后,再切膠、破膠成小塊;減少生膠中的水分含量,避免在后續(xù)加工過程中產(chǎn)生氣泡。
2.橡膠配合劑處理:液態(tài)配合劑如松焦油、古馬隆等,需要加熱、熔化、蒸發(fā)水分、過濾雜質(zhì),并進行干燥處理;塊狀配合劑如石蠟、硬脂酸、松香等要粉碎,粉狀配合劑若含有機械雜質(zhì)或粗粒時需要篩選除去;粉狀配合劑篩選去除機械雜質(zhì)或粗粒,減少可能的水分來源;確保配合劑在混煉過程中能夠均勻分散,減少因水分引起的問題。
3.適量使用吸濕劑:適量使用氧化鈣等吸濕劑,吸收原膠、再生膠和配合劑中的水分,減少硫化時產(chǎn)生氣泡的風險。氧化鈣還可以作為填充材料,增加橡膠制品的容積并改善物理機械性能。
4.合理設(shè)計模具:設(shè)計合理的模具,確保在成型過程中膠料能夠順暢流動,減少因壓力不均導致的水分滯留。
5.塑煉工藝:對再生膠進行適當?shù)乃軣?,進一步提高膠料可塑性、滲透性和成型流動性,使得配合劑更容易均勻分散,同時有助于排除膠料中的水分。
6.混煉工藝:控制再生膠混煉工藝參數(shù),如溫度、壓力、時間等,確保再生膠與配合劑充分混合,混煉機的機械拌合作用應(yīng)使配合劑完全、均勻地分散在再生膠中,避免局部水分過高。監(jiān)控混煉過程中的生產(chǎn)參數(shù),以確保產(chǎn)品質(zhì)量的穩(wěn)定性和一致性。
7.硫化工藝:再生膠制品硫化過程中,嚴格控制溫度、時間和壓力等參數(shù),確保橡膠能夠充分硫化或固化,獲得所需的強度和耐久性,同時去除多余的水分。
8.成型工藝:再生膠制品在成型過程中,控制模具的溫度和壓力,確保膠料能夠順暢流動并充滿模具,減少因水分引起的氣泡。
9.環(huán)境控制:保持生產(chǎn)環(huán)境的干燥和通風,避免因環(huán)境濕度過高而導致橡膠材料吸收水分。
10.中間檢查:在生產(chǎn)過程中的各個階段進行中間檢查,如混煉膠的門尼粘度測試,以監(jiān)控水分含量是否在控制范圍內(nèi)。
11.后處理:硫化后的橡膠制品應(yīng)進行適當?shù)暮筇幚恚缧捱?、清洗等,以去除可能殘留的水分?/p>
控制再生膠制品生產(chǎn)過程中的水分含量對提高產(chǎn)品的質(zhì)量和性能有重要意義;此外部分橡膠配合劑反應(yīng)也會產(chǎn)生水分,比如氧化鋅與硬脂酸反應(yīng)的副產(chǎn)物有水,后續(xù)繼續(xù)與您探討相關(guān)問題。
獨家原創(chuàng)文章【商業(yè)授權(quán)】無書面授權(quán)禁止任何形式轉(zhuǎn)載,摘抄、節(jié)選。關(guān)注鴻運橡膠:學習再生橡膠生產(chǎn)橡膠制品的工藝配方和原料的技術(shù),幫您降低成本增加利潤。