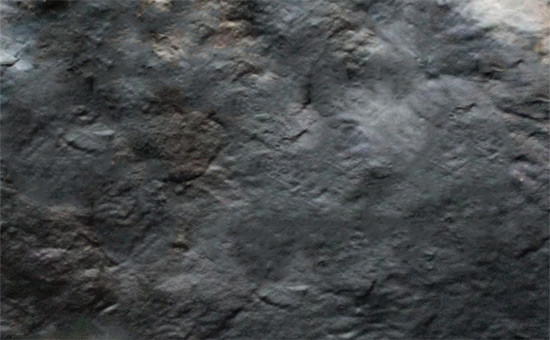
焦燒是膠料在存放和加工過程中由于熱量積累產(chǎn)生的早期硫化現(xiàn)象,導(dǎo)致橡膠制品表面不光亮、有皺紋、表面不平,且材質(zhì)變脆易裂。焦燒的主要原因是硫化體系選擇不當(dāng)或硫化劑、促進(jìn)劑用量不合理。以再生膠為主要原料生產(chǎn)橡膠制品時,合理設(shè)計硫化體系,提高再生橡膠的焦燒安全性至關(guān)重要,尤其是在生產(chǎn)過程中需要長時間加工的再生橡膠制品。
1. 注意再生膠硫化劑與促進(jìn)劑的配合
再生膠制品硫化配方中,選擇在加工溫度下反應(yīng)速度較慢的硫化劑,嚴(yán)格控制硫化劑的用量,避免過量使用導(dǎo)致過早焦燒。優(yōu)先配合遲效性或臨界溫度較高的促進(jìn)劑;合理搭配促進(jìn)劑和活化劑(如氧化鋅、硬脂酸等),以達(dá)到最佳的硫化效果和焦燒性能。
2. 硫化促進(jìn)劑選擇要點與焦燒性能
提高再生膠焦燒安全性需要在選擇促進(jìn)劑時優(yōu)先考慮硫化促進(jìn)劑的焦燒性能。建議選擇含有防焦官能團(tuán)(-SS-)和輔助防焦基團(tuán)(羰基、羧基、磺?;?、磷酰基、硫代磷?;?、苯并噻唑基)的促進(jìn)劑E4LYY124。比如,次磺酰胺類促進(jìn)劑焦燒時間長、硫化速度快、硫化曲線平坦、綜合性能較好,加工安全性好,適用于再生膠厚制品硫化。
各種促進(jìn)劑的焦燒時間依下列順序遞增:ZDC < TMTD < M < DM < CZ < NS < NOBS < DZ。在實際應(yīng)用中,再生膠制品可以采用幾種類型促進(jìn)劑并用的體系,以達(dá)到最佳的硫化性質(zhì)和加工安全性。
3. 促進(jìn)劑并用 提高再生膠焦燒安全性
(1)使用秋蘭姆類促進(jìn)劑硫化的再生膠膠料配方,減少秋蘭姆促進(jìn)劑用量,并與次磺酰胺類或噻唑類促進(jìn)劑并用,可以延長焦燒時間。
舉個例子:促進(jìn)劑TMTD硫化誘導(dǎo)期短,可使膠料快速硫化,當(dāng)TMTD作為主促進(jìn)劑使用時,與次磺酰胺類或噻唑類促進(jìn)劑并用,可以延長焦燒時間;避免將促進(jìn)劑TMTD與促進(jìn)劑D或二硫代氨基甲酸鹽并用,否則會降低再生膠膠料的耐焦燒性。
(2)胍類促進(jìn)劑熱穩(wěn)定性高,比如促進(jìn)劑D,作為主促進(jìn)劑,膠料焦燒時間長,硫化速度慢。
(3)天然橡膠/再生膠并用生產(chǎn)橡膠制品時,噻唑類和次磺酰胺類促進(jìn)劑與DTDM配合可以提高膠料抗焦燒性。
(4)丁基橡膠、丁基再生膠制品硫化體系中選擇二硫代氨基甲酸鹽類促進(jìn)劑,對焦燒安全性更有利。含有促進(jìn)劑TMTD和氧化鋅的氯化丁基橡膠、氯化丁基再生膠膠料中配合使用氧化鎂或促進(jìn)劑DM,可以延長膠料焦燒時間。
再生膠制品生產(chǎn)中合理選擇硫化劑、促進(jìn)劑的品種,嚴(yán)格控制其用量,可以有效提高再生膠焦燒安全性。在實際生產(chǎn)中,補強(qiáng)劑、填充劑、軟化劑品種,再生膠硫化條件等都會影響焦燒安全性,后續(xù)繼續(xù)與您討論相關(guān)問題。
獨家原創(chuàng)文章【商業(yè)授權(quán)】無書面授權(quán)禁止任何形式轉(zhuǎn)載,摘抄、節(jié)選。關(guān)注鴻運橡膠:學(xué)習(xí)再生橡膠生產(chǎn)橡膠制品的工藝配方和原料的技術(shù),幫您降低成本增加利潤。