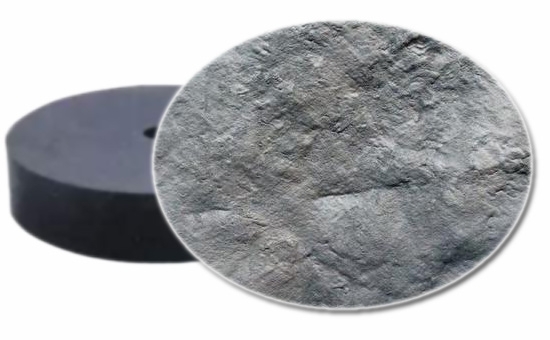
焦燒是橡膠加工過程中或硫化前停放過程中發(fā)生的早期硫化現(xiàn)象,即自硫,橡膠制品生產中經常遇到的一個問題,使用防焦劑可以有效避免膠料焦燒。使用再生膠生產橡膠制品時,硫化劑、促進劑、補強劑、填充劑、甚至于防老劑都會影響膠料焦燒安全性,不同品種的配合劑對再生膠焦燒安全性影響不同,再生膠制品廠家需要合理調整配方中的配合劑種類與用量。
1.硫化體系配合劑影響再生膠焦燒安全性
使用再生膠生產橡膠制品時,配方中硫化劑、促進劑用量過多、硫化體系配合不合理是導致膠料焦燒的主要原因,其中促進劑的種類與用量對再生膠焦燒安全性影響很大,不同品種的促進劑對膠料加工安全性影響不同,橡膠制品廠家需要根據(jù)橡膠促進劑的種類選擇合適的防焦劑,比如使用次磺酰胺類促進劑的再生膠制品配方中使用防焦劑HTM可以有效避免再生膠焦燒問題出現(xiàn)。
2.補強體系配合劑影響再生膠焦燒安全性
炭黑、白炭黑是再生膠制品生產中常用的補強劑,由于細粒子炭黑與白炭黑在再生膠混煉過程中分散困難、生熱快,會明顯增加膠料焦燒發(fā)生的幾率,用量越大、焦燒時間越短。對于炭黑產品來講,高結構度的炭黑會縮短再生膠焦燒時間,含氧量高、ph值低的酸性炭黑焦燒時間較長如槽法炭黑;可見炭黑的結構性、表面酸堿性以及含氧量等都會影響再生膠制品的焦燒安全性。
因此再生橡膠制品廠家使用炭黑或白炭黑2LLYY429補強時,一定要選擇合適品種的炭黑、白炭黑,控制補強劑用量,必要時減少補強劑用量,既能夠減小焦燒傾向、又能夠降低一定的原料成本。
3.防老體系配合劑影響再生膠焦燒安全性
合理的防老體系設計對提高再生膠制品耐老化性能、延長制品使用壽命有重要意義。然而在實際生產中,不同種類的防老劑對焦燒影響不同,有些防老劑可以預防焦燒。一般情況下,酮胺類防老劑、喹啉類防老劑,如常見的防老劑RD、防老劑AW有促進焦燒的作用;對苯二胺類防老劑對焦燒有一定的促進作用,不同品種的對苯二胺類防老劑對焦燒促進作用不同,常見的有防老劑TMDQ、防老劑DPA、防老劑DNPD和防老劑DAPD等。
值得一提的是,防老劑264、防老劑2246在再生膠制品生產中可以起到一定的防焦作用,而通用型防老劑D 對再生膠焦燒性能幾乎無影響,推薦使用。
使用再生膠生產橡膠制品時,軟化劑、填充劑對膠料焦燒性能影響不大。橡膠制品廠家一定要選擇合適品種的配合劑配合,除了使用防焦劑之外,還可以適當增加硬脂酸等酸性物質用量,在不影響硫化速度的前提下減緩焦燒速度。提高膠料焦燒安全性、避免焦燒可明顯提高再生膠制品質量與成品率,降低原料成本、避免不必要的經濟損失。
獨家原創(chuàng)文章【商業(yè)授權】無書面授權禁止任何形式轉載,摘抄、節(jié)選。關注鴻運橡膠:學習再生橡膠生產橡膠制品的工藝配方和原料的技術,幫您降低成本增加利潤。